ENTOC
The next stage in virtual engineering and commissioning

- Project
start
September 2016 - Project
end
Aug 2019 - Project
leader
Thomas Bär,
Daimler Buses
EvoBus GmbH, Germany - More
information
https://itea4.org/project/entoc.html
Engineering is the most time-consuming aspect of innovation and products are increasing in complexity, yet there has not been a corresponding growth in the number of people involved in production facility planning. Due to the reduction in cycle times needed to remain competitive, combined with highly individualised products and the fact that one changed parameter can affect many other areas, problems in the line can have serious time and cost consequences for businesses.
The 2020 award-winning project ENTOC, gathering 11 partners from Germany and Sweden, minimises the time and effort involved in engineering without compromising on reliability or integrity by formalising specification requirements for production equipment and establishing standardised mechatronic component models. This project is a follow-up of the ITEA project AVANTI, also led by Daimler, which had already received an award in 2017 for its outstanding results.
Reducing engineering time and effort
Production equipment creation currently begins with the specification of requirements, which engineers bring together manually in different types of text documents for suppliers. The main goals of the project were to develop standardised modelling strategies and to optimise the engineering tool chain used for complex production plants. ENTOC improved the information flow for new production equipment by sharing information and improving the workflow.
One of ENTOC’s primary innovations is the generation of a formalised specification of requirements that enables the automatic creation of proposals for car/truck manufacturing and machine building.
In a joint effort to cover and formalise large parts of requirements specifications, each partner covered different types of requirements, which were combined by means of a common data model exchanged in the AutomationML data format. Production resource planning was covered by tarakos, process-driven production planning by Daimler, product variability by Chalmers, project planning by ifak, and requirements expressed in natural language by TWT. Whereas the current state-of-the-art is completely manual, ENTOC has achieved a 30% requirements formalisation rate. Using the concept of formalised requirements, the time for the creation of production equipment specifications can be reduced up to 20%, improving the quality in parallel.
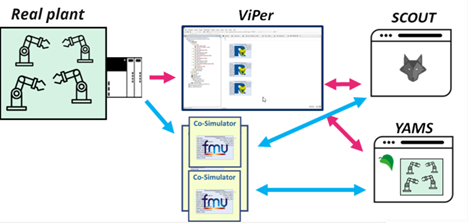
In addition, ENTOC has shown that component behaviour can also be standardised. The results used the standard FMI, which is currently under discussion in the production context and is being investigated/adapted by automation software vendors and multiple OEMs for production. Thus, it was also integrated in the international standard for exchanging engineering information (AutomationML modelling concept – WP Part 6 AutomationML component including referenced FMUs, (see Figure 1).
Component manufacturers, e.g. Festo, provide Functional Mockup Units (FMUs) as added value to their production components. These behaviour models may be exchanged directly (as files) or integrated/ provisioned via a digital store, e.g. provided by vendors like CADENAS. Currently, direct exchange is the most common method.
Whereas simulation models were previously used solely in virtual commissioning (the practice of using technology to create a simulation model to enable testing of the proposed changes and upgrades before they are implemented), these models can be reused and maintained across different production phases, providing feedback for the requirements definition stage and generating a full digital loop.
Changing the face of manufacturing
ENTOC’s success lies in the fact that it opens doors, changing the face of manufacturing as its innovations are picked up in the wider market. Efficiency is key.
Standardised component behavioural descriptions and models can be easily exchanged between companies, reducing the need to re-engineer existing know-how and thus reducing overhead. Across all manufacturing domains, engineering process chain duration can thus be reduced by up to 10% for the creation time of virtual production models, leading to greater competitiveness.
ENTOC’s success lies in the fact that it opens doors, changing the face of manufacturing as its innovations are picked up in the wider market.
Commercialisation is ongoing for most partners and two tools are already available on the market. As software and engineering companies, EDAG and EKS have benefited enormously from the development results of the ENTOC Project.
EKS is using the rfCSPy FMI cosimulator – one result of the ENTOC project – in combination with their RF::SUITE for virtual commissioning and digital twins. This serves as basis for the virtual plant and corresponding analytic tools of EKS (focusing on e.g. cycle times, collisions, etc.) and creates competitive advantages for the adopters of the standard FMI. The FMI standard allows not only the inclusion of component behaviour but also other aspects such as the analysis of energy consumption.
Hybrid virtual commissioning is now possible – the mix of black box FMU behaviour models from component vendors and traditional white box behaviour models which require significant effort for creation. This is supported within the EKS tools but, as one impact of ENTOC and the first market pressure, other software tools like SIMIT and WinMOD are now supporting FMUs too.
Based on the ENTOC results, the company in2sight launched the product game4automation. The game4automation tool is a digital twin framework based on game technology. It enables simulation and virtual commissioning, including an FMU interface.
In addition to integrating FMUs in engineering and simulations platforms, PLCConnect (see Figure 2) and its post- ENTOC results developed master co-simulation which has enabled the user-friendly incorporation of FMUs into NX Mechatronics Concept Designer and as Co-Simulation with TwinCAT, SIMIT and WinMOD. The wide usage of FMUs in conjunction with digital twins and virtual commissioning was made possible with the introduction of PLCConnect’s master co-simulation.
EDAG has already sold this solution to Small and Medium-Sized Enterprises (SMEs) and large industrial customers; this allowed EDAG to take on at least two additional employees for further development and consulting. Through consulting, several of our customers have integrated FMUs as part of their virtual commissioning tool chain. EDAG is in regular contact with ENTOC partner Festo in order to continuously integrate their FMU components in joint customer projects.
EKS has a platform where new approaches can be realised as prototypes (such as in ITEA projects like SPEAR, TESTOMAT and XIVT) and virtual commissioning pilot projects can be started using FMUs. There are two main benefits:
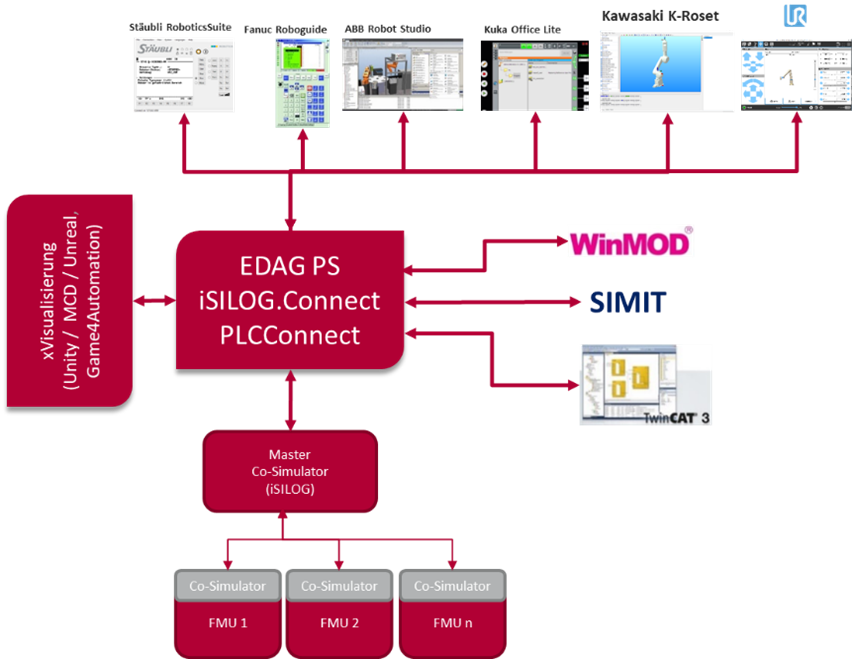
- The behaviour models are closer to reality. The more precise models (provided by component manufacturers because of their knowledge about the component) increase the quality of the simulation results, e.g. a more accurate process analysis, including process time prognosis during virtual commissioning.
- simulation models decreases by several hours up to several days depending on the complexity of the component. This was a market opener, especially for small and medium-sized companies which do not possess the necessary resources. For a typical mid-sized virtual production station, the effort for creating the virtual commissioning model can be reduced from 20 days to 12 days, additionally improving the effort needed for quality checks.
For all providers, ENTOC also safeguards intellectual property while boosting reputation: formalised descriptions are made for components, providing a quality guarantee for endusers, and a black box set-up prevents the underlying functions from becoming public knowledge. Based on formalised descriptions of component models and various tools that support them, virtual commissioning is now also affordable for SMEs.
To lay the foundations for future innovations, ENTOC is now pursuing IEC standardisation. Within the project, OEMs, tool providers and component manufacturers agree that this is the next stage in virtual engineering and commissioning. In recognition of this, most ENTOC partners are still working on the topics in the ongoing ITEA project AIToC, which combines requirements engineering and Artificial Intelligence in the tool chain to further extend the efficiency, quality and adaptability of manufacturing. A new success story in the making?
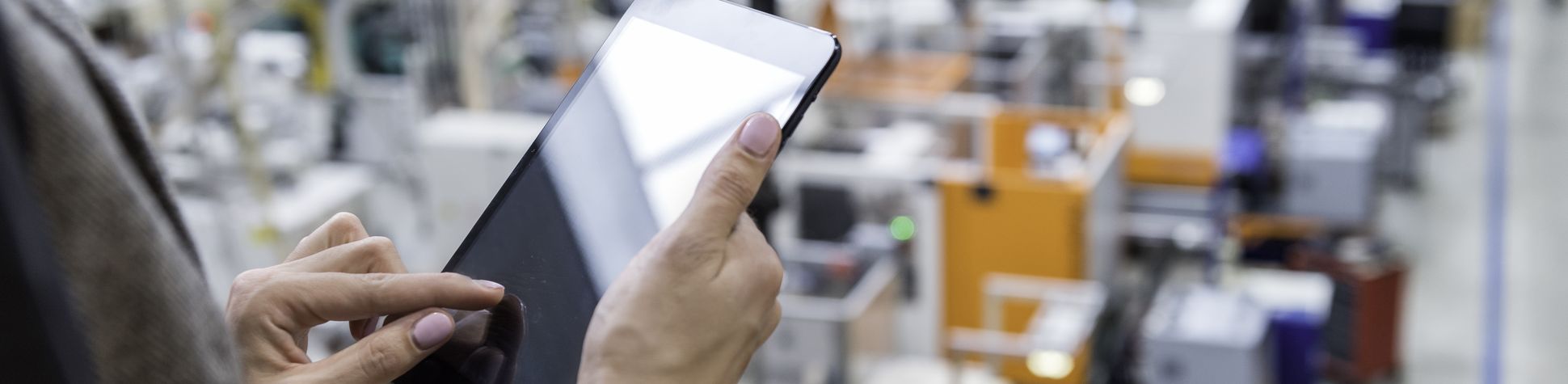
Other chapters
Use the arrows to view more chapters
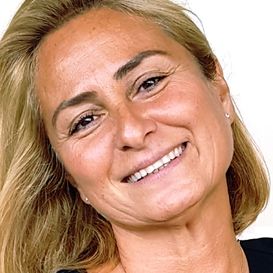
Editorial
By Zeynep Sarılar
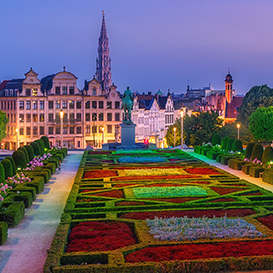
Country Focus: Belgium
Creating jobs through innovation
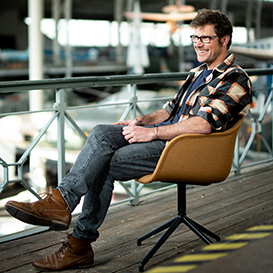
FEops
Becoming a truly global player
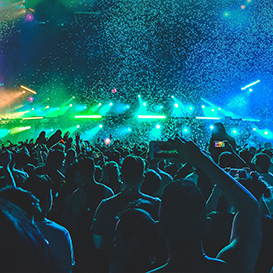
ITEA Success story: MOS2S
New forms of engagement in entertainment and society
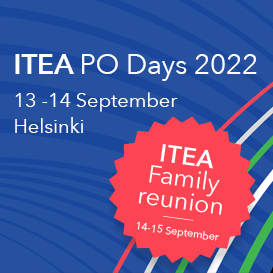
ITEA PO Days 2022 & ITEA Family reunion
The ITEA Community is coming together again!
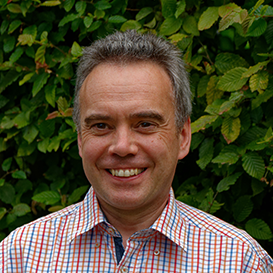
Community talk with Olivier Biot
An internationalist in body and soul
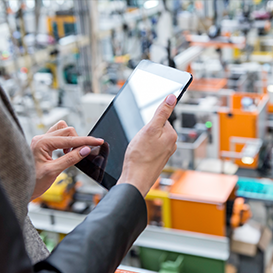
ITEA Success story: ENTOC
The next stage in virtual engineering and commissioning
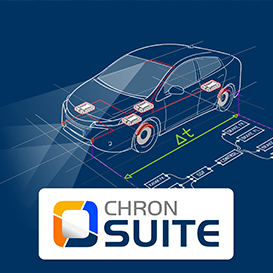
SME in the spotlight: INCHRON
A passion for finding the right timing
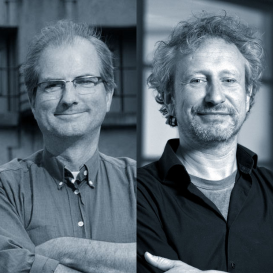
By and for end-users
Improving quality of life for patients and professionals alike
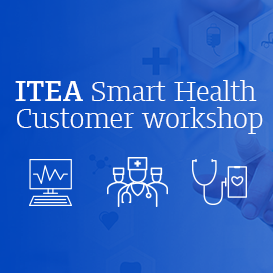
Smart health – new challenges ahead!
Insights into the 2022 Smart health customer workshop
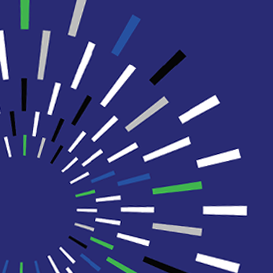
Introducing the ITEA Call 2021 projects
A promising start!
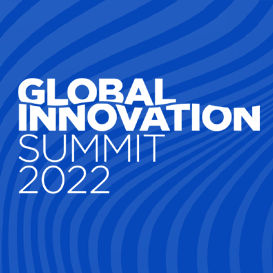
Global Innovation Summit 2022
Good to meet again, in-person and online