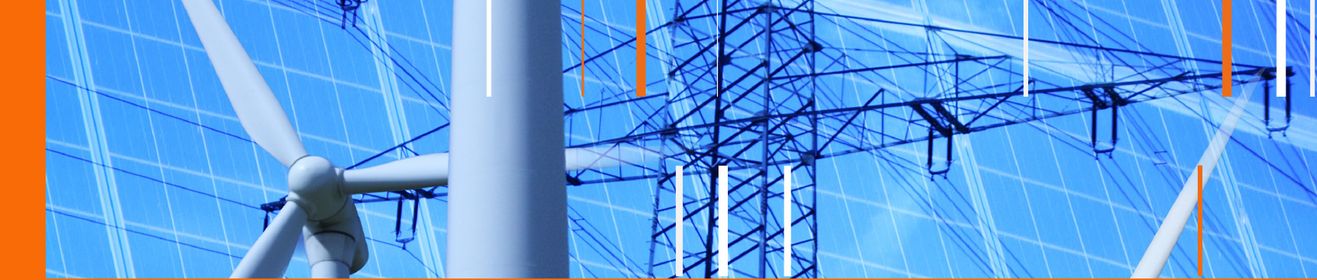
ITEA Impact story
MODRIO
Digital twins for the safe and efficient design and operation of cyber-physical systems






Impact highlights
- OpenModelica has been used in ABB’s Optimax Powerfit product to generate optimising control code that controls and coordinates about 5000 MW (approx. 7.5%) of German electricity production within seconds. This has subsequently been expanded to about 6000 MW.
- Vattenfall used the results to optimise the start-up of conventional power plants, with an estimated yearly gain of €850k per plant.
- Knorr-Bremse developed a new braking system that allows to reduce by 30% the hardware tests, which are generally very resource consuming. In addition, this braking system can reduce the safety margins between trains and thus enable more efficient use of the track. In turn, the flow of trains and passengers can be improved – by between 5 and 14%, depending on the type of traffic.
- For EDF, which uses results regarding the modelling of requirements to automate the FMEA (Failure Modes, Effects and Criticality Analysis) of safety critical systems, the expected gains are estimated to be around 30% of the cost of large projects.
- For Dassault-Aviation, MODRIO has enabled many very useful breakthroughs for the design of next-generation aircraft, in particular the results regarding the modelling of requirements and system architecture, associated with fast multi-core simulations, multi-mode modelling of system failures and safety analysis. Output from ITEA projects like MODRIO has brought Dassault-Aviation capabilities that allow different working methods to handle complex systems, thereby contributing to the global (digital) transformation of the company.
Cyber-physical systems (CPS) are very large systems that not only involve a large number of stakeholders but
are safety critical and have significant impact on the economy and the environment as well. This makes tools
for the safe and efficient design and operation of such systems imperative. The ITEA project MODRIO, which
ran from 2012 to 2016, was set up to extend modelling and simulation tools based on open standards (Modelica
and FMI) from system design to system operation. The main technological ambition of the project was to
provide an integrated modelling and simulation framework able to efficiently specify, design and operate
CPS. To that end, new ideas were developed to address the complete engineering lifecycle, from preliminary
design to operation and maintenance.
Project results
New features include the formal modelling of requirements involving objects, sub-systems, systems and human interactions in space and time in order to automate system design verifications. With optimisation of the operation of large transients such as start-ups or shutdowns or the evaluation of the consequences of faults and failures in mind, a new modelling approach was developed. The aim was to provide the ability to simulate the system behaviour away from its nominal operating point when transitions between modes, represented by completely different sets of equations, take place. One key success factor was the involvement of large industrials whose businesses are to design and operate large CPS in four major industrial domains: energy (electricity production, transmission and distribution), aerospace (civil aircraft), transportation (trains) and buildings. Other key factors were to base tool development on two existing standards, Modelica and the FMI together with the participation of all prominent players in those two standards, in terms of standard and tool development. Finally, the project benefited from the cooperation between SMEs and research organisations.
Exploitation
One of the main early achievements was the ability to generate software code for optimising the control of 6000W, representing almost one tenth of German electrical power production. Up to 1500 MW comes from more than 2500 small solar and wind power generators that are coordinated to operate as a single big power plant.One of the main early achievements was the ability to generate software code for optimising the control of 6000W, representing almost one tenth of German electrical power production. Up to 1500 MW comes from more than 2500 small solar and wind power generators that are coordinated to operate as a single big power plant.
Vattenfall used the results to optimise the start-up of conventional power plants, necessitated by the rising share of renewable energy production that forces conventional power plants to manoeuvre more frequently to balance the grid, while complying with all operational constraints in order to satisfy safety and environmental regulations and minimise system wear.
In the rail domain, the industrial cooperation partners – Knorr-Bremse and Bombardier Transportation – focused the results on crosswind stability and friction brakes. To boost the potential of brake distance management, Knorr-Bremse uses FMIs extensively to share simulation models between stakeholders. This makes it possible to simulate the behaviour of the entire system of a passenger train at a very early stage of development.
EDF uses results regarding state estimation to detect and diagnose the causes of power losses in power plants. A new power loss monitoring system, which combines physical modelling with Modelica and Bayesian networks and modelling based on neural patterns, is now deployed in the nuclear power plant EDF fleet, and has prompted the launch of a new start-up to provide model-based smart diagnosis and prognosis services for CPS.
The roots of EMBrACE, a follow-up ITEA project in which 45 organisations across 8 countries have declared interest to develop a new standard and associated tools for the formal modelling and simulation of requirements, can be found in MODRIO that produced the draft specifications for a new requirement modelling language. Finally, ideas developed in MODRIO about multi-mode modelling were among the incentives behind the development of a new modelling language, named MODIA by Modelica founders, that could be the successor to the Modelica language in the long term.
More information
Download MODRIO impact storyRelated projects
MODRIOOrganisations
ABB (Germany)ABB AB (Sweden)
Dassault Aviation (France)
Electricité De France (France)
Katholieke Universiteit Leuven (Belgium)
Knorr-Bremse (Germany)
Vattenfall (Sweden)