
Eindhoven, 9 September 2020
The next stage in virtual engineering and commissioning
Second award for Daimler-led ITEA project on Smart Manufacturing
Today, ITEA Vice-chairman Philippe Letellier has handed over the ITEA Award of Excellence in the category Innovation to ENTOC project leader Thomas Bär, manager at Daimler Buses. ENTOC minimises the time and effort involved in engineering without compromising on reliability or integrity, by formalising specification requirements for production equipment and establishing standardised mechatronic component models. This project is a follow-up of the ITEA project AVANTI also led by Daimler, which was already awarded in 2017 for its outstanding results.
Engineering is the most time-consuming aspect of innovation and products are increasing in complexity. Yet there has not been a corresponding growth in the number of people involved in production facility planning. Due to the reduction in cycle times needed to remain competitive combined with highly individualised products and the fact that one changed parameter can affect many other areas, problems in the line can have serious time and cost consequences for businesses.
Reducing engineering time and effort
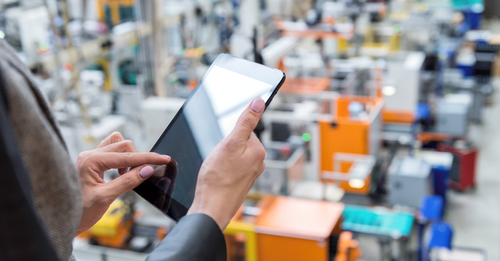
The ITEA project ENTOC, gathering 11 partners from Germany and Sweden, minimises the time and effort involved in engineering without compromising on reliability or integrity. Production equipment creation currently begins with the specification of requirements, which engineers bring together manually in different type of text documents for suppliers. The main goals of the project were to develop standardised modelling strategies and to optimise the engineering tool chain used for complex production plants. ENTOC improved the information flow for new production equipment by sharing information and improving the workflow. One of ENTOC's primary innovations is the generation of a formalised specification of requirements that enables the automatic creation of proposals for car/truck manufacturing and machine building.
In addition, ENTOC has shown that component behaviour can also be standardised. The resulting standard is currently being incorporated into an external platform for the creation of a digital store in which component models can be purchased from various providers. Whereas simulation models were previously used solely in virtual commissioning (the practice of using technology to create a simulation model to enable testing proposed changes and upgrades before they are actually implemented), these models can be reused and maintained across different production phases, providing feedback for the requirements definition stage and generating a full digital loop.
The key value of ENTOC is the holistic approach to information flows, spanning the hole value chain of production engineering. This would not have been possible without the support of ITEA, as it facilitates exchange and transition within the community, enabling the development of a 'simulation strategy' across different projects. The roots of this project can be traced back to the ITEA project MODELISAR, which started in 2008 and future projects can benefit from the archived standardised description of information in this domain.
- Thomas Bär, Manager at Daimler Buses
Changing the face of manufacturing
ENTOC's success lies in the fact that it opens many doors, changing the face of manufacturing as its innovations are picked up in the wider market. Part of this is adaptability for companies: if the feedback loop shows that one model is more popular, production can quickly be extended. Efficiency is also key. Whereas the current state-of-the-art is completely manual, ENTOC has achieved a 30% requirements formalisation rate. This should lead to an up to 30% reduction in documenting efforts for OEMs such as Daimler and Volvo. Furthermore, standardised component behavioural descriptions and models can be easily exchanged between companies, reducing the need to reengineer existing know-how and thus reducing overhead. Across all manufacturing domains, engineering process chain duration can thus be reduced by up to 10%, leading to greater competitiveness.
Yet another success story in the family of ITEA projects in modelisation & simulation. The production line is often the last wheel of the design process while it has such an impact on the success of a product. With ENTOC, Daimler and the other ENTOC partners invest in a level of abstraction to allow an optimised design of the production lines. They do it in a standardised way allowing all the value chain stakeholders to join this effort in their own interest. A great success of the collaborative spirit we observe in the ITEA projects.
- Philippe Letellier, ITEA Vice-chairman
Within the project, OEMs, tool providers and component manufacturers agree that this is the next stage in virtual engineering and commissioning. In recognition of this, most ENTOC partners are working on a new ITEA proposal which will combine requirements engineering and Artificial Intelligence in the tool chain to further extend the efficiency, quality and adaptability of manufacturing. A new success story in the making?
More information:
https://itea3.org/project/entoc.html
Project supported by:
- BMBF
https://www.softwaresysteme.pt-dlr.de/de/itea.php - Vinnova
https://www.vinnova.se/en/calls-for-proposals/eureka-cluster-financing/itea-3--software-intensive-systems-and-2020-03027/
Download press release:
WORD format
Note for editors, not for publication
For interview requests, questions and additional information about ITEA and ENTOC, please contact:
ENTOC Contact person
Thomas Bär, Daimer Buses - Global coordinator
thomas.baer@daimler.com
Johan Vallhagen, Volvo Group - Swedish coordinator
johan.vallhagen@volvo.com
Matthias Riedl, IFAK - German coordinator
matthias.riedl@ifak.eu
ITEA Contact person
Linda van den Borne-Toupet
linda.van.den.borne@itea3.org
About ENTOC project partners
The ENTOC project has been conducted by a German and a Swedish cluster. The partners were selected to cover and master different roles; with theory, new technology opportunities, industrial needs and challenges in the manufacturing engineering value chain. Thus, based on mixed skills, expertise and experiences provided by the research and technology providers and with the needs and demands from industrial OEM partners, it has been possible to reach an innovative level through well focused research work and application of research results.
The ENTOC project has been actively managed to facilitate a close cooperation between partners on international level to fully utilise the potential of every partner's capabilities and contributions. Another important factor has been the definition of different types of industrial use-cases to develop, test and demonstrate the results and validated for different types of production systems.
German partners
- Daimler - Felix Auris
- EDAG Production Solutions - Ali Moghaddam Nejad
- EKS InTec - Anton Strahilov
- FESTO - Bernd Kärcher
- IFAK - Matthias Riedl
- tarakos - Klaus Hanisch
- TWT Science & Innovation - Ireneus Wior
Swedish partners
- Algoryx Simulation - Kenneth Bodin
- University of Technology Chalmers - Petter Falkman
- Schneider Electric Sweden - Peter Gronwall
- Volvo Group - Johan Vallhagen
About ITEA
ITEA is the Eureka Cluster programme for software innovation, enabling a large international community to collaborate in funded projects that turn innovative ideas into new businesses, jobs, economic growth and benefits for society.
It covers a wide range of business opportunities facilitated by digitisation like smart mobility, healthcare, smart cities and energy, manufacturing, engineering and safety & security. ITEA pushes important technology fields like artificial intelligence, big data, simulation and high-performance computing into concrete business applications.
ITEA is open to large industry, small and medium-sized enterprises (SMEs), start-ups, academia and customer organisations. Its bottom-up project creation ensures that the project ideas are industry-driven and based on actual customer needs.
https://itea3.org