ACOSAR
An innovative simulation that saves time and money

The development of vehicles has become increasingly complex, involving over 50 different suppliers who need to ensure that all components, parts and devices work together. Modelling and simulation represent key methods for a successful development. To facilitate this, the introduction of co-simulation methodologies and the interoperability of simulation tools and infrastructure had already taken root. But there was no standardised way of integrating distributed simulation and test environments back in 2015. So there was still room to enhance the process.
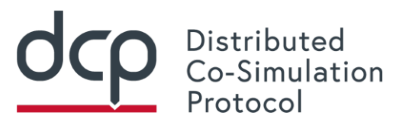
In the ACOSAR project, 16 partners came together under the lead of VIRTUAL VEHICLE in order to accelerate development steps with new simulation technologies. With a strong focus on the automotive domain, the consortium’s members operated on all levels of the automotive supply chain and included original equipment manufacturers (OEMs), suppliers, software tool and real-time system vendors, as well as research and academic partners.
Early predictions and correspondingly early design decisions are key success factors in modern development processes. With the aid of co-simulation, diverse simulation models can be linked together to enable overall system analysis at a very early stage of development (‘front loading’). Within the virtual system development, front loading is getting more and more important in a plenitude of industrial domains to reduce development times, stranded costs and time-to-market. Cosimulation is a particularly promising approach for interoperable modular development. However, the coupling and integration of realtime systems into simulation environments (especially of systems of distributed Hardwarein- the-Loop (HiL) systems and simulations) still require enormous effort. ACOSAR developed both a non-proprietary ‘Distributed Co-simulation Protocol’ (DCP) for Real-Time (RT) System integration and a corresponding integration methodology, which is a substantial contribution to the international standardisation (Modelica Association Project DCP - MAP DCP).
Standardised Distributed Co-simulation Protocol
Impact highlights
- Since July 2018, the main and sustainable project outcome the Distributed Co-simulation Protocol (DCP) is developed as a Modelica Association Project (MAP) and is available as an open-access international standard.
- International technology leaders such as AVL, Volkswagen and Boeing are already applying this solution.
- prominent German sports car manufacturer reports over 13,000 developer days which could be saved in the next five years thanks to this developed protocol – which corresponds to a value of around five to seven million euros.
- In the final year of the ACOSAR project the DCP was adopted by the Modelica Association.
- The international partner network of VIRTUAL VEHICLE now consists of 30 national and 50 international industrial partners (OEMs, Tier 1 and Tier 2 suppliers as well as software providers) as well as 18 national and 30 international scientific institutions.
The DCP is an application level communication protocol. It is designed to integrate models and real-time systems into simulation environments. It enables the exchange of simulation-related configuration information and data by use of an underlying transport protocol (such as User Datagram Protocol (UDP), Transmission Control Protocol (TCP), or CAN). At the same time, the DCP supports the integration of tools and realtime systems from different vendors.
DCP has the potential to simplify and accelerate integration aspects for system development by blurring the boundaries between purely virtual and real tests. International technology leaders such as AVL, Volkswagen and Boeing are already applying this solution. A prominent German sports car manufacturer reports over 13,000 developer days which could be saved in the next five years thanks to this developed protocol – which corresponds to a value of around five to seven million euros.
Transfer of results into standardisation was one of the key goals of ACOSAR. In the final year of the project, the consortium members therefore decided to pursue standardisation of the DCP with the Modelica Association. Since July 2018 the DCP has been developed as a Modelica Association Project (MAP), also with VIRTUAL VEHICLE in the lead. The DCP specification document 1.0 was released in March 2019, as an open-access Modelica Association standard. The DCP complements an existing set of standards for system simulation, including the Modelica Language, the Functional Mock-Up Interface (FMI), and the System Structure and Parameterisation (SSP) standard.
All these efforts have received broad international recognition. During the ITEA Project Outline Preparation Days 2019, ACOSAR received an Award of Excellence for its outstanding project results, especially on standardisation and communication. On top of this distinction, ACOSAR was presented with an additional Eureka Award during the subsequent Eureka Stakeholder Conference.
For project coordinator VIRTUAL VEHICLE, the success of the project was another milestone in its 15 years of experience in the field of simulation technologies. This focus on industryrelated research makes VIRTUAL VEHICLE the innovation catalyst for future vehicle technologies. The international partner network of VIRTUAL VEHICLE now consists of 30 national and 50 international industrial partners (OEMs, Tier 1 and Tier 2 suppliers as well as software providers) in addition to 18 national and 30 international scientific institutions.
For instance, ESI Group implements DCP for its system simulation solutions. ESI expects to significantly increase the interoperability of its tools and a reduction of development and maintenance costs due to the replacement of several tool specific co-simulation modules by the standardised and tool-independent DCP.
Impact beyond the project
The range of applications is wide and can, for example, reduce the setup and configuration time. A typical example can be found in the field of automated driving where new sensor technologies are becoming available and must be tested before real prototypes are used for selected test scenarios. Further applications gaining benefit from the DCP are typically found in the fields of distributed simulation, cosimulation, hardware-, software-, or model-inthe- loop testing, and process automation
The results of ACOSAR will lead to a modular, considerably more flexible and shorter system development process for numerous industrial domains as well as enable the establishment of new business models.
More information
Other chapters
Use the arrows to view more chapters
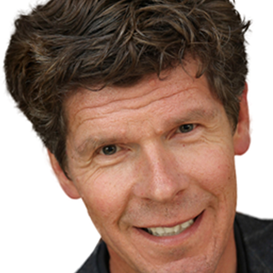
Editorial
By Jan Jonker

Country Focus: Canada
Connecting companies to enable access to new markets and global value chains
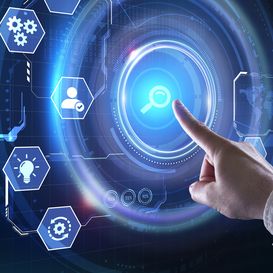
QA Consultants
Future-proofing our company
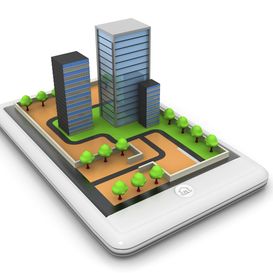
ITEA Success story: C³PO
C³PO democratises City Planning
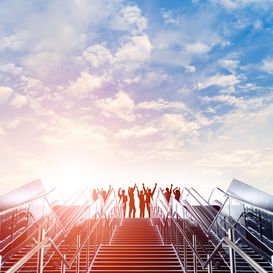
Viewpoint on entrepreneurship
Innovare - to make new again
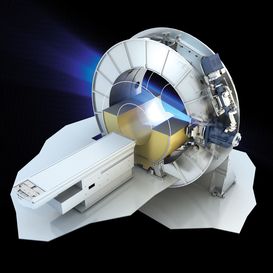
End user happiness: SoRTS and STARLIT
Tumour in sight during radio treatment
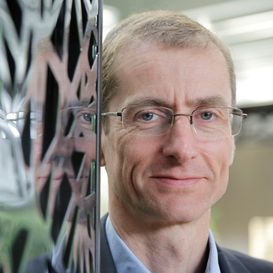
New ITEA Vice-chairman: Jean-François Lavignon
The new helmsman at the wheel
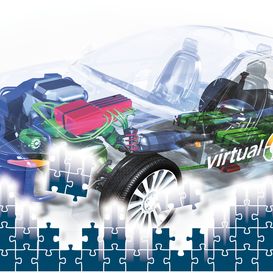
ITEA Success story: ACOSAR
An innovative simulation that saves time and money
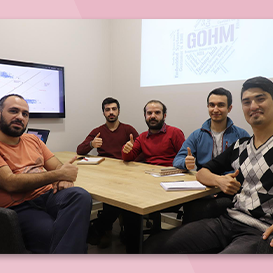
SME in the spotlight: GΩHM
Embedded intelligence to improve quality of life
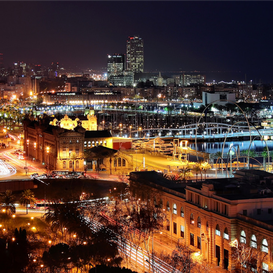
The Smart City Business Event
The Road to Smart City Live
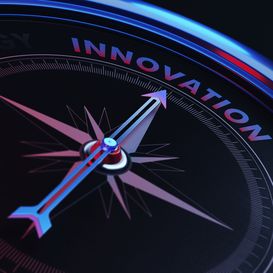
State of the Art
A compass for your projects
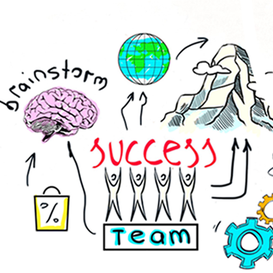
Online ITEA PO Days
ITEA Community clearly showed its agility at the Online ITEA PO Days 2020