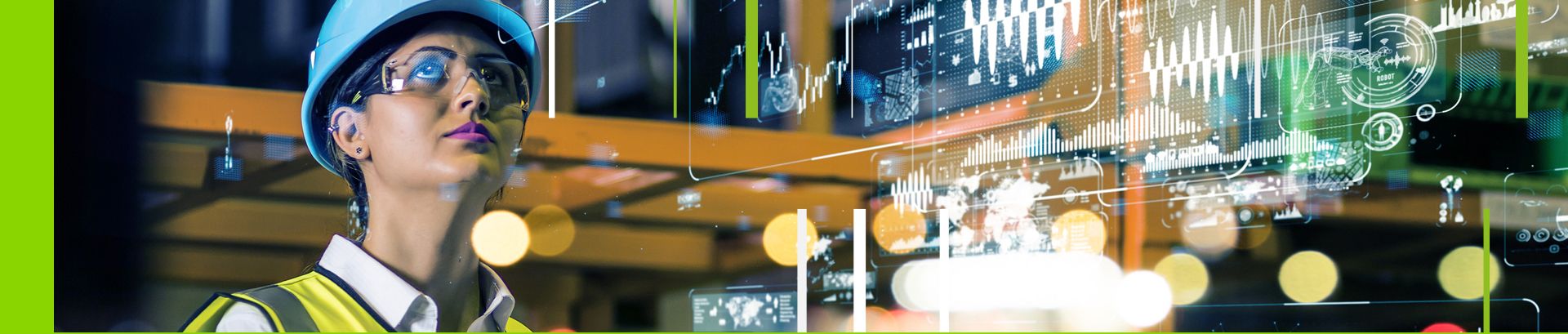
ITEA Impact story
PIANiSM
Pioneering predictive maintenance for a smarter future in manufacturing




Impact highlights
- Portuguese project partner and plastic film manufacturer Vizelpas has experienced a strong impact at an operational level as the company has successfully improved both the mean time between failure (MTBF) and the time taken to repair equipment; MTBF increased by 15.8% and the mean time to repair (MTTR) decreased by 11%.
- Turkish Refinery operator Tüpraş has applied KoçSistem’s technical outputs of the PIANiSM project to its heater charge pumps, resulting in a decrease in mean time to repair by 3.59 days and a decrease in maintenance costs by USD 5,134 per failure.
- Since the PIANiSM’s completion, Canadian SME B3 Systems has acquired over 20 new clients across various industries, such as automotive, mining, and manufacturing. The company has also expanded its reach into new geographical markets, including North America, Europe, and Asia. This expansion has driven significant revenue growth and increase in workforce over the past two years.
- Over the next five years, the consortium anticipates a strong sales increase through the introduction of PIANiSM related technologies (including roughly 100% sales growth for companies in manufacturing and 80% for IT and software), as well as a more than doubling of the international market share in some sectors.
Predictive maintenance (PdM), using data-driven, proactive maintenance techniques designed to analyse the condition of equipment and helping to predict when maintenance should be performed, offers benefits across many fields, from manufacturing to mining to automotive. By predicting issues before they occur, companies avoid wasting time and money on repairs and downtime, allowing them to be more efficient throughout their operations. However, most of these solutions are domain or problem-specific, with implementation costs and complexity serving as obstacles to uptake. To disrupt traditional maintenance processes, domains such as data science, machine learning, analytics, simulation and real-time processing must be combined in one system.
The ITEA project PIANiSM, uniting 14 partners from Canada, Portugal, Spain and Türkiye, aimed to merge predictive and prescriptive maintenance techniques to achieve an end-to-end automated manufacturing process and optimise end-to-end manufacturing value chains. In doing so, it has identified and introduced missing analytics techniques and algorithms and introduced a new generation of data identification integration and modelling processes.
Project results
PIANiSM's backbone lies in the developed architecture, a sophisticated framework comprising four layers for data acquisition, data pre-processing, model development and applications. Using this architecture, PIANiSM’s technical partners have each developed separate solutions for exploitation. Since the most important focus of the PIANiSM project is the predictive maintenance concept, it was of great importance to have diverse data sets that include different countries and sectors. For this reason, the project involved nine different use-case partners.
Exploitation
Thanks to PIANiSM, KoçSistem has supplemented its existing big data platform, Platform 360, with a PdM module that uses techniques such as data mining and model management to produce predictive maintenance reports, failure prediction and maintenance plans. A big automotive customer, that was already using Platform 360 before, has purchased the PdM module after the PIANiSM project.
Thanks to the updated Platform 360, the accuracy ratio of fault detection at this customer increased up to 84%, meaning the customer had information about these faults before they occurred and enabling the organisation to take the needed precautions in time.
Introducing a collaborative framework integrating data science, machine learning, and real-time processing within PIANiSM, Turkish SME ERSTE enhanced predictive maintenance in manufacturing. Leveraging the insights, ERSTE advanced further in other RD&I projects including ITEA project MACHINAIDE, and extended AutoML-powered solutions for streamlined equipment maintenance decisions.
Portuguese plastic film manufacturer Vizelpas supplied production and equipment data for the development of ISEP's predictive maintenance algorithms and enhanced Sistrade's monitoring tools, providing manufacturing expertise and feedback as required – all with a high degree of interaction and strong spirit of collaboration within the international consortium. This resulted in a set of algorithms and tools that could provide predictive insights and reports on equipment usage and maintenance to improve Vizelpas' equipment awareness capabilities. A strong impact has since been felt at an operational level as the company has successfully improved both the mean time between failure (MTBF) and the time taken to repair equipment. Increasing the uptime of equipment means a greater ability to meet the demands of customers, with a knock-on reduction in maintenance costs and a smaller parts inventory. From a human perspective, this also allowed Vizelpas to divert human resources away from manual equipment control and maintenance to higher value tasks.
Within PIANiSM, B3 Systems developed customised algorithms that not only predict equipment failures but also prescribe preventive measures, thereby reducing downtime and maintenance costs. This capability has enabled manufacturers to transition from traditional, reactive maintenance strategies to proactive, predictive approaches.
For instance, clients have reported a reduction in unplanned downtime by up to 40% and maintenance cost savings of 20-30%, significantly enhancing operational efficiency and productivity. The success of the PIANiSM project has positioned B3 Systems as a leader in the predictive maintenance domain.
Overall, PIANiSM has produced use-cases on ceramics, automotive, energy/ refineries, durable consumer goods, piping, plastic film/flexible packaging and data networks and has successfully demonstrated its system prototypes in an operational environment (TRL 7).
More information
Download PIANiSM Impact storyRelated projects
PIANiSMOrganisations
B3 Systems Inc. (Canada)ERSTE Software Limited (Türkiye)
KoçSistem (Türkiye)
SISTRADE Software Consulting, S.A. (Portugal)
Tupras-Turkish Petroleum Refineries (Türkiye)
VIZELPAS - COMÉRCIO DE ARTIGOS PLÁST…
Vestel (Türkiye)